It looks like you're new here. If you want to get involved, click one of these buttons!
Guys,
I have a project here that requires holding down all components upon a small printed circuit board, flipping it over and soldering the contact points from the backside.
I abhor the concept of doing this to each and every component individually and hoping that a third hand I do not possess called gravity will be sufficient to produce a consistent product.
I have come up with a jig I call the 3rd-Hand which uses foam blocks of varying thicknesses to create a mating surface for all the components and apply equal pressure upon them to keep them tight to the board so I can install the components, install the 3rd-Hand (snap it into place), flip the board/assembly and solder all the components from the backside at one time/pass and do another repetitively and get paid for this effort.
Do any of you guys have experience in this area?
Pics - later - left the phone at the house . . .
Comments
Search Amazon for “helping hands” and see what you find. If you want to be fast, bend the leads slightly to make some spring tension against the hole to help hold the parts in place.
https://en.wikipedia.org/wiki/Wave_soldering
You can stake the component in place by bending the leads and solder with solder paste and a hot air rework tool.
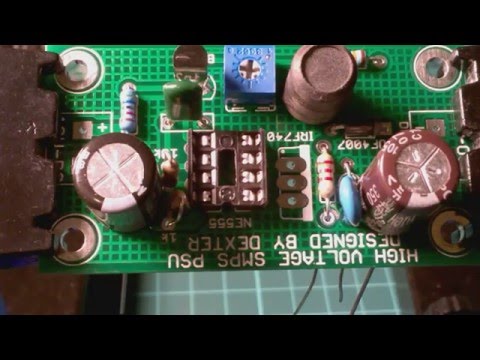
I'm not really able to bend-over the leads as the solder pads are small and round and will look badly if done this way. This is why I am making a component hold-down jig and clamp assembly.
The Hot Air tool is interesting and a very good idea when soldering in cold environments like I will be doing part time - it heats the board as well as the connection point making cold solder joints far less likely to form.
Do these tools [Hot Air Gun] work with standard 60/40 wire solder as well?
A hot air gun is not what is used here. Something like a hot air desoldering system from MetCal is what is required.
InDIYana Event Website
Maybe still clamp it into a foam sheet to press the parts into the board, but just do it in stages depending on the part height? Starting with the shallowest parts like resistors and diodes and working your way up from there. That sounds like a nice balance of simple but effective. Depends on the specific project though I suppose.
Drew, I think your idea makes a lot of sense and would make the assembly of the hold-down system more simple - I just have to do everything from soup-to-nuts - If I can't see the end result with all the steps covered in one pass I get tangled up in starting on a good enough solution.
There are several different [size/parts configuration] boards I have to make a hold-down system for and it is taking forever to get the 1st one built.
The key to the whole process is manufacturing the actual clamping device . . .
How many boards will be assembled?
If not many, I have used masking tape to hold the components in place, quick and dirty.
50 per month of various configurations . . .
Have you contacted any board houses? There is one in Appleton WI I used when I was at Danfoss. About 100 boards per order (month). I couldn't believe how cheap they were compared to what we estimated our cost was to stuff and solder each PCA's.
This is part time work in my retirement and I get paid by the hour for doing this instead of paying a board assembling house. I'd love to send it out but that cuts me out of my play money income. Thanks for the thoughts though.
Gotcha. I didn't realize what you were up to.
Back in the day we did pretty much what Ken's video showed with inserting the components and bending the leads out to almost 30 degs to keep them from falling out. We didn't use solder paste and a reflow/rework gun though. We had a dozen or so ladies sitting at work benchs with their Weller soldering stations and rolls of Kester 60/40 0.031" solder. Back in the 80's those gals probably didn't make much more than $6/hr and a lot developed carpal tunnel syndrome and/or serious arthritis
Not to mention lead poisoning.
Most companies use lead free stuff now.
Yeah maybe from the fumes. We didn't have smoke suckers back then. But we were really strict about wearing latex gloves and zero food, drink, or candy at their work stations. They got unlimited breaks to get up and stretch their legs, use the bathroom, etc.
I've thought about all of these hazards and will take the necessary precautions/ventilation - thanks for pointing them out though. I have enough aches and pains as it is . . .
https://www.digikey.com/en/maker/projects/how-to-build-a-solder-reflow-oven/6c52df4782084f8d97c62d1349df058f
As long as the components can take the heat this would save you a lot of labor and no need to flip the boards.
Any tool that gets over 650° will melt solder. This is the hot air tool I have at home. YIHUA 959D-Digital Hot Air Rework Station, High Power with 3 Memories, Airflow Efficiency, °F /°C Display, Accurate Temp.(212°F~932°F), Brushed Aluminum Panel & Safety Features https://a.co/d/9lPGdwg
We use Pace and Quick at work. The Quick are cheap but have held up pretty well. They do have a REALLY dirty power supply that affects other equipment on the circuit.
Thanks for the links, Ron.
Running a toaster oven could get a bit expensive on energy costs . . . and melt the relay cases on these boards.
Mad as a hatter with carpel tunnel looks like my future.
Atleast use one of those fans with the filter on it. Every time I solder up crossovers I get a nice headache the next day. Probably making me dumber each time.
Yes, Drew - I keep looking at them but they are not really an effective device for removing the nasties from the air in a closed/conditioned space. Looks like I will need to cut a hole in the side of the building over the location best suited to be used as a soldering station.
Solder fumes do not contain lead, but they do contain chemicals from flux/rosin.
Steve - look for a small air purifier. I have one in my office from Amazon (because there was mold in a wall) but I realized when I was soldering that it would work great so I keep it near by. I also have a stack of N95 masks and I can throw one of those on if I am feeling particularly nervous about the fumes.
This is great information a4e!!
A small multi-stage carbon HEPA filter system with a little added door cracking for ventilation could work just fine when the outdoor temps are above 35* because I use a 2 ton mini-split VSD Heat pump for space conditioning in ~800 sq ft.
I also have mold problems this year due to the never ending rain of the past 3 years and the subsequent arachnid infestation along with sinus problems.
I just need to investigate filter media further at this point since I have plenty of fans (FCAF - Forward Curved Air Foil) for the air movement and can build the frames to support the filter media . . .
Mine didn't last very long. The hot air still works but the soldering iron started acting erratic and even after replacing the soldering iron, it refuses to get to temp and read right.
Good to know KB - thanks for chiming-in.
I have a Stahl soldering iron that has worked well for several years now but am new to the air heated unit concept.
With the Asian equipment we have had fail a lot of it has been connection or craftsmanship issues not bad/broken components. It would not surprise me if it was a simple fix. You may also consider checking the handpiece, the heating elements fail often and I know others have had DOA handpiece.
I am lucky to have a Hakko soldering station. They make great equipment.
If electrical components are not considered consumer level and non-recyclable they probably still use lead based solder. I would argue the Chinese are likely not using lead-free on a wide scale, either.
Lead based solder just offers too many advantages on a mass production scale.
Echo the sentiments about inhalation of fumes. The occasional crossover job is one thing, but when you plan on sitting for hours around the stuff evacuation from the area is probably important. A simple DIY booth should suffice, can be built with a couple muffin fans and a large cardboard box. That will get it out of direct inhalation paths but lighting will be a concern at that point, I suppose.
You can buy carbon filers pretty easily. Get some 20*20 and put them on a box fan. A fume extractor close to the point of smoke is a good idea as well.
Some progress tonight since I feel more energetic . . .
Uses spring loaded self closing cabinet hinges to grasp board after pressing into position.
Counterproductive heat exchange around windows mitigated - sealed air gaps - no pics.
Soldering Fume Exhaust method figured out conceptually - will utilize existing dust collection system vented to exterior via 4" hose with throttled blast gate and open wood stove door to draw-in make up air at low volume from existing 6" flue pipe.