I just looked up home anodizing on YouTube, bunch of videos on how to do it. You can get the battery acid at AutoZone, I bought a lead roof flashing at the Depot for the in tank conductor, and a power supply. It took a few tries to get it right. My take is the aluminum has to be super fucking clean. I bought the dye from an anodizing company and it was in the dye for prolly two weeks to get that deep red. Also got the sealer that company offered, although straight boiling water apparently works too.
What JR said, smack them out with a punch. Have something to catch it. I had one bounce back and hit the cone on the RS10's I did. I just super glued it back in.
I polished the ones on the 442's
@6thplanet said:
I just looked up home anodizing on YouTube, bunch of videos on how to do it. You can get the battery acid at AutoZone, I bought a lead roof flashing at the Depot for the in tank conductor, and a power supply. It took a few tries to get it right. My take is the aluminum has to be super fucking clean. I bought the dye from an anodizing company and it was in the dye for prolly two weeks to get that deep red. Also got the sealer that company offered, although straight boiling water apparently works too.
Thanks for the details. I looked at youtube, quite a few videos on it. I will most probably start a new thread for this. But any video / link that you found simple and straight to the point. I'' start byt collecting all the materials needed.
Yes, Type II anodizing is done in a sulfuric acid solution (basically battery acid at 40% by volume). The important part is to keep the solution below 68 F. A lead cathode like you did works really well. Aluminum is safer and works great but it requires more electrical current.
After dye we do a hot nickel acetate seal at 205 F. The color dye process should only take 10 mins, but that depends on the dye chemistry and temperaure.
For a power supply you only need 24 Vdc or less and about 40 amps per square foot. So those little pole pieces only need a couple of amps.
The surface prep prior to anodizing is probably the most important part. Junk in junk out...
To long ago to remember exact videos, just watched some and had at it. The dye process for me was a bit difficult ad I really didn't have a way to keep the dye solution warm, so it was get it warm then let it sit. It worked fine, just took awhile. The sealer was some chemical added to boiling water. You can see the voltage and current that was happening in my pic. Craig knows this stuff as he works with it, I just rigged some shit up to see if it'd work.
Comments
Ani -
If you don't want to machine the outrigger try this link: https://8020.net/etcatalogsearch/search/keydesresult/?etkeydes=Extended+Straight+Structural+Pivot+Arm.
Reasonable prices, black and aluminum finishes and different lengths available. I got this from Dan Neubecker and have used them.
I just looked up home anodizing on YouTube, bunch of videos on how to do it. You can get the battery acid at AutoZone, I bought a lead roof flashing at the Depot for the in tank conductor, and a power supply. It took a few tries to get it right. My take is the aluminum has to be super fucking clean. I bought the dye from an anodizing company and it was in the dye for prolly two weeks to get that deep red. Also got the sealer that company offered, although straight boiling water apparently works too.
What JR said, smack them out with a punch. Have something to catch it. I had one bounce back and hit the cone on the RS10's I did. I just super glued it back in.
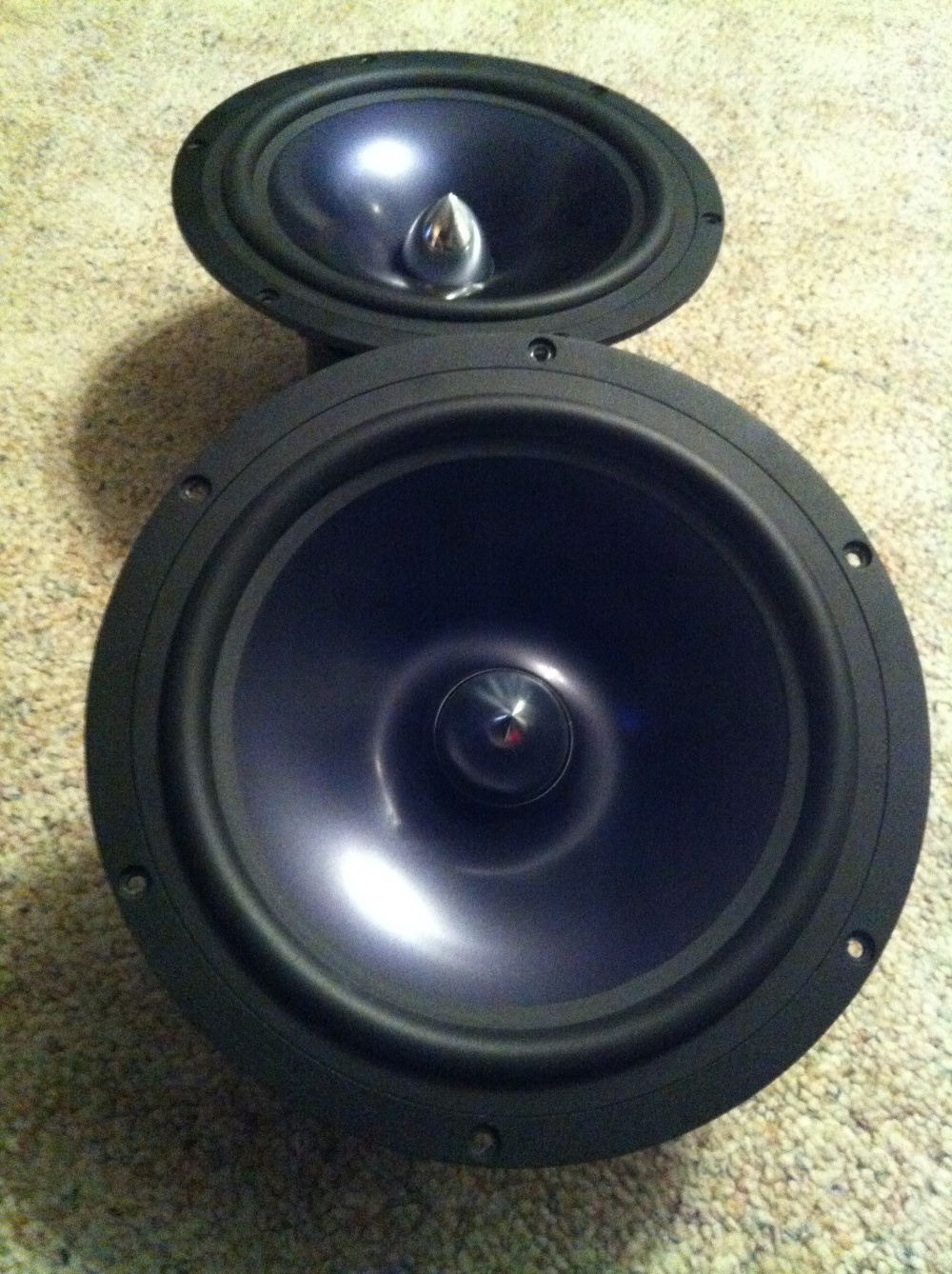
I polished the ones on the 442's
Thanks for the details. I looked at youtube, quite a few videos on it. I will most probably start a new thread for this. But any video / link that you found simple and straight to the point. I'' start byt collecting all the materials needed.
Yes, Type II anodizing is done in a sulfuric acid solution (basically battery acid at 40% by volume). The important part is to keep the solution below 68 F. A lead cathode like you did works really well. Aluminum is safer and works great but it requires more electrical current.
After dye we do a hot nickel acetate seal at 205 F. The color dye process should only take 10 mins, but that depends on the dye chemistry and temperaure.
For a power supply you only need 24 Vdc or less and about 40 amps per square foot. So those little pole pieces only need a couple of amps.
The surface prep prior to anodizing is probably the most important part. Junk in junk out...
To long ago to remember exact videos, just watched some and had at it. The dye process for me was a bit difficult ad I really didn't have a way to keep the dye solution warm, so it was get it warm then let it sit. It worked fine, just took awhile. The sealer was some chemical added to boiling water. You can see the voltage and current that was happening in my pic. Craig knows this stuff as he works with it, I just rigged some shit up to see if it'd work.