I'm about ready to order, going with RSS265s 4ohm, but HO vs HF?
In a 3-way looks that both are good for LP ~400Hz or less. The HF maybe a bit smoother, but HO designed for a smaller enclosure 0.6ft^3 vs HF 0.9ft^3, yet with eq (and my previous testing of a woofer in a small, and smaller sealed boxes) I don't think either would be an issue. Leaning towards the HO (providing a smaller box design), UNLESS anyone knows of issues with this driver vs. its' HF design ??? Thx
Looking for woodworking suggestions as I venture far away from a rectangular box. My latest drawing incorporates one curved (kerfed) side and an additional hurdle with the front baffle tilted back approximately 4 degrees relative to the rear. So at the bottom depth ~ 8.5 inches tapered to top depth 6 inches (height ~32 inches). The base area sealed, the top section open to rear for the coax.
My initial thoughts- after cutting the sides, and kerfing the one (longer) side, then attaching these to the cut-to-size baffle. By adding an additional ¼ in (or so) to the sides depth for flush trimming later. After set up, placing the framed piece onto the rear board - pencil outline and cut back the width of the sides to set inside at the required angle (slope relative to front baffle) leaving the ~ ¼ inch to later flush trim the sides down to the inset back.
This may be a leap of faith for me - but I’m up to a challenge. Seeing extensive woodworking skills on many projects here - I’m asking for suggestions. Thanks.
Yes, I'm targeting ~32 (to 33) inches (with the tilt back baffle to aim the coax a bit upward toward listening ear height).
I haven't played with sketch-up for quite a while, but will be giving it a go > especially to pull the pre-kerfed side's dimensions - which is the wild card here (determining the length isn't a big deal, its the tapering from the base to the top as its curve changes around the woofer towards flat at the top.
updated edit: Best for me with this one to start with some corrugated cardboard and duct tape, before I start cutting Baltic Birch
I had just placed a decent sized order for a couple of drivers (going with Morel woofers), a few electrical odds and ends (connectors), and denim/mat damping material... and asked if there was a discount coupon they could possibly apply. I didn't have one, have been an ok customer over the years, but what the heck > I asked. And they 'found one' and applied a discount credit to my order. Not expected, but certainly appreciated.
I was just wondering if you have ever played with 1/2 inch 3 ply plywood sheathing? It would easily conform to your bend without kerfing. It is unsanded so it is very rough.
@Eggguy said:
I was just wondering if you have ever played with 1/2 inch 3 ply plywood sheathing? It would easily conform to your bend without kerfing. It is unsanded so it is very rough.
I haven’t, but thanks I’ll take a look. I could also possibly use two ¼ in ply and glue/ clamp to a mold or clamp around a pre-cut baffle. But I’m definitely going to start with heavy cardboard knowing that the front baffle being angled in towards the top will be a ‘stretched’ version of the back and the sides are unique as well. I may have to simplify - but hopefully not.
I’ve been playing with sketchup, confirming an angle of the front baffle tilt-back with my old- style graph paper (~12.5 feet to listening, ctr coax 27in to ear height 42 in seated @ 4.2 to 4.5 degrees. So if base depth 8.5 inches top depth ~6 to 6 ⅛ inch. Surprisingly, sloped front baffle total height w/in ⅛ in of rear panel. ‘Course every panel is different (side vs side, front baffle vs back, and top vs bottom- although parallel the dimensions differ). I’ve got a few ideas as to the build steps, but again thinking the cardboard mockup will show me something I’m missing. My winter project.
@Kornbread said:
Cardboard mock up ... m thinking fiberglass resin, maybe some glass and make it permanent, if you like the mock up.
I didn't post a picture of my hands / fingers the last time I tried spray adhesive for interior sound deadening material. Lets just say imagine fuzzy dice...
But interestingly, maybe a carbon fiber look +++. I was thinking of wrapping the sides in black grill cloth to get a Vandersteen look with wood cap and base, but maybe carbon-fiber veneer (if available as a veneer?).
Edit: apparently there is. Anyone worked with this stuff?
Have you seen how folks can try to use a thickness planer as a jointer by shimming the piece against another flat board? I'm wondering if you could do something similar on the table saw.
Attach the enclosure shell (curved side down) on a sacrificial board with shim blocks that prevent the piece from rocking. It would be attached at the desired cut angle. The sacrificial board provides the straight edge that would ride along the fence. Success would depend on the depth of your bend compared to max depth of cut of the table saw.
@DrewsBrews said:
Have you seen how folks can try to use a thickness planer as a jointer by shimming the piece against another flat board? I'm wondering if you could do something similar on the table saw.
Attach the enclosure shell (curved side down) on a sacrificial board with shim blocks that prevent the piece from rocking. It would be attached at the desired cut angle. The sacrificial board provides the straight edge that would ride along the fence. Success would depend on the depth of your bend compared to max depth of cut of the table saw.
Thanks, possibly. I'll be interested at looking at the curved side (post mock-up) as to whether it tapers from the base depth to the top depth evenly from one end to the other. Hopefully so. If so, then I can first attach (as bending) to/under the front baffle (with mounting pins / guide edge first placed under baffle) with a slight baffle 'overhang' to come back and flush-trim. The kerfed bend, if kerfed spacing consistent, should provide a smooth bend and hence smooth curve for the baffle.
They look great! I have four of those 830668's and have wanted to try something similar to what you did. Did cavity resonances determine how high you could cross the woofers? Sorry for the thread hijack Andy.
I started this thread looking at a full open back, and good info here. I'm sticking with open back for the coaxial and going sealed for the bottom end.
The Elves made an early delivery.
These are beasts, and should have little issue with a bit of eq in a sealed design. At only 84.7dB @2.83v/1m it's a good thing each gets its own amp channel 325/650w.
I’m considering using black walnut for the top cap and base (neither structural to the build) and just looked at pricing. I’m thinking the good stuff (with lots of character in the boards) qualifies as a precious commodity. Jeez.
While the one with a curved side (cardboard baffle mock-up) works to keep width relative to drivers (6.5 coaxial / 10.35 W at base), the design is battling my left brain… which prefers an old ~Naim design (with width set per woofer).
While I generally like curve sided speakers, my own left brain really likes the Niam look too, the light wood colored one. The all black one kind of looks like a guitar half stack (amp) to me.
Comments
Women talk . . . a lot . . .
I'm about ready to order, going with RSS265s 4ohm, but HO vs HF?
In a 3-way looks that both are good for LP ~400Hz or less. The HF maybe a bit smoother, but HO designed for a smaller enclosure 0.6ft^3 vs HF 0.9ft^3, yet with eq (and my previous testing of a woofer in a small, and smaller sealed boxes) I don't think either would be an issue. Leaning towards the HO (providing a smaller box design), UNLESS anyone knows of issues with this driver vs. its' HF design ??? Thx
Looking for woodworking suggestions as I venture far away from a rectangular box. My latest drawing incorporates one curved (kerfed) side and an additional hurdle with the front baffle tilted back approximately 4 degrees relative to the rear. So at the bottom depth ~ 8.5 inches tapered to top depth 6 inches (height ~32 inches). The base area sealed, the top section open to rear for the coax.
My initial thoughts- after cutting the sides, and kerfing the one (longer) side, then attaching these to the cut-to-size baffle. By adding an additional ¼ in (or so) to the sides depth for flush trimming later. After set up, placing the framed piece onto the rear board - pencil outline and cut back the width of the sides to set inside at the required angle (slope relative to front baffle) leaving the ~ ¼ inch to later flush trim the sides down to the inset back.
This may be a leap of faith for me - but I’m up to a challenge. Seeing extensive woodworking skills on many projects here - I’m asking for suggestions. Thanks.
Is the height less than 48?
Yes, I'm targeting ~32 (to 33) inches (with the tilt back baffle to aim the coax a bit upward toward listening ear height).
I haven't played with sketch-up for quite a while, but will be giving it a go > especially to pull the pre-kerfed side's dimensions - which is the wild card here (determining the length isn't a big deal, its the tapering from the base to the top as its curve changes around the woofer towards flat at the top.
updated edit: Best for me with this one to start with some corrugated cardboard and duct tape, before I start cutting Baltic Birch
KUDOS to Parts Express: Kim and Lisa !
I had just placed a decent sized order for a couple of drivers (going with Morel woofers), a few electrical odds and ends (connectors), and denim/mat damping material... and asked if there was a discount coupon they could possibly apply. I didn't have one, have been an ok customer over the years, but what the heck > I asked. And they 'found one' and applied a discount credit to my order. Not expected, but certainly appreciated.
And yes, I thanked them both.
I was just wondering if you have ever played with 1/2 inch 3 ply plywood sheathing? It would easily conform to your bend without kerfing. It is unsanded so it is very rough.
I haven’t, but thanks I’ll take a look. I could also possibly use two ¼ in ply and glue/ clamp to a mold or clamp around a pre-cut baffle. But I’m definitely going to start with heavy cardboard knowing that the front baffle being angled in towards the top will be a ‘stretched’ version of the back and the sides are unique as well. I may have to simplify - but hopefully not.
I’ve been playing with sketchup, confirming an angle of the front baffle tilt-back with my old- style graph paper (~12.5 feet to listening, ctr coax 27in to ear height 42 in seated @ 4.2 to 4.5 degrees. So if base depth 8.5 inches top depth ~6 to 6 ⅛ inch. Surprisingly, sloped front baffle total height w/in ⅛ in of rear panel. ‘Course every panel is different (side vs side, front baffle vs back, and top vs bottom- although parallel the dimensions differ). I’ve got a few ideas as to the build steps, but again thinking the cardboard mockup will show me something I’m missing. My winter project.
Cardboard mock up ... m thinking fiberglass resin, maybe some glass and make it permanent, if you like the mock up.
I didn't post a picture of my hands / fingers the last time I tried spray adhesive for interior sound deadening material. Lets just say imagine fuzzy dice...
But interestingly, maybe a carbon fiber look +++. I was thinking of wrapping the sides in black grill cloth to get a Vandersteen look with wood cap and base, but maybe carbon-fiber veneer (if available as a veneer?).
Edit: apparently there is. Anyone worked with this stuff?
Have you seen how folks can try to use a thickness planer as a jointer by shimming the piece against another flat board? I'm wondering if you could do something similar on the table saw.
Attach the enclosure shell (curved side down) on a sacrificial board with shim blocks that prevent the piece from rocking. It would be attached at the desired cut angle. The sacrificial board provides the straight edge that would ride along the fence. Success would depend on the depth of your bend compared to max depth of cut of the table saw.
Thanks, possibly. I'll be interested at looking at the curved side (post mock-up) as to whether it tapers from the base depth to the top depth evenly from one end to the other. Hopefully so. If so, then I can first attach (as bending) to/under the front baffle (with mounting pins / guide edge first placed under baffle) with a slight baffle 'overhang' to come back and flush-trim. The kerfed bend, if kerfed spacing consistent, should provide a smooth bend and hence smooth curve for the baffle.
I've used the adhesive backed carbon fiber sheet. It works like any other PSA veneer. This was a carbon/copper weave.
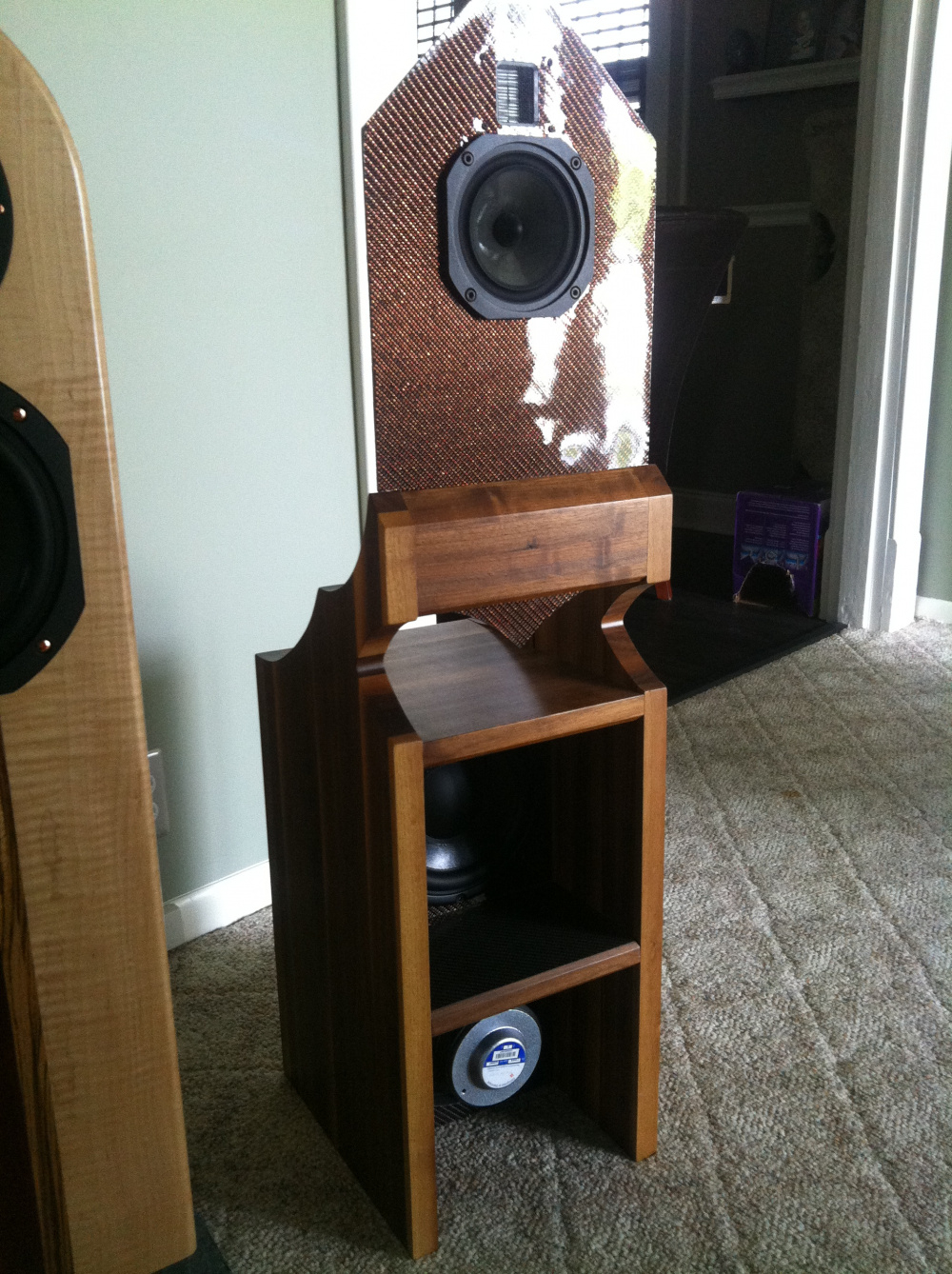
Are those the Peerless 830668? If yes, how was the dipole bass?
Was gonna ask same thing on the H frame bass
They have they're limit, but within it's limit, not bad! That speaker is for easy listening levels, not rocking out.
They look great! I have four of those 830668's and have wanted to try something similar to what you did. Did cavity resonances determine how high you could cross the woofers? Sorry for the thread hijack Andy.
No problem.
I started this thread looking at a full open back, and good info here. I'm sticking with open back for the coaxial and going sealed for the bottom end.
Yes, as is the con of an H frame. It's a balance of gain and upper frequency limit.
The Elves made an early delivery.
These are beasts, and should have little issue with a bit of eq in a sealed design. At only 84.7dB @2.83v/1m it's a good thing each gets its own amp channel 325/650w.
1058's, nice! Haven't heard a set of those yet...
InDIYana Event Website
How do we find/contact these elves?
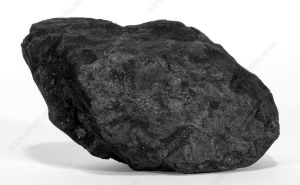
I also got an early delivery, but it was just this lump of coal...!
I do love me some Morel
I’m considering using black walnut for the top cap and base (neither structural to the build) and just looked at pricing. I’m thinking the good stuff (with lots of character in the boards) qualifies as a precious commodity. Jeez.
Dang! Those look the bee's knees🤘🏼
Left Brain vs. Right Brain
While the one with a curved side (cardboard baffle mock-up) works to keep width relative to drivers (6.5 coaxial / 10.35 W at base), the design is battling my left brain… which prefers an old ~Naim design (with width set per woofer).
Make them shaped like a woman instead . . . 36, 26, 34 . . . centimeters . . .
My physics teacher in HS had this poster with ‘Think Metric’ (with appropriate metric measurements). Got me thinking metric…
While I generally like curve sided speakers, my own left brain really likes the Niam look too, the light wood colored one. The all black one kind of looks like a guitar half stack (amp) to me.