@Bill - you can use a little dental proxa brush or a q-tip and coat the insides of the driver mounting holes with yellow glue to avoid any thread stripping. I'm a big fan of tung oil finishes, but I think these would look nice with a clear finish. You could try some wipe-on poly on some scrap. The variation in that pine grain is mind blowing on some pieces.
But Chahly - Stahkist don't want speakers that look good, Stahkist wants speakers that sound good!
I have found that having a box fan or two blowing directly on the work pieces cuts the oil's dry time in half, at least. I also turn the work pieces every few hours. I was able to topcoat some hickory with lacquer only 3 days after applying the last coat of boiled linseed oil.
Good idea. Not sure if I am going to stain or oil the wood, but if I do, I will give that a try. Even if I leave the wood natural without sealer, oil or anything else, hitting it with lacquer will cause roughness on the first few coats, due to a chemical reaction with the wood itself. I like to sand down the first few coats with 220 until the lacquer starts to build into a very smooth finish.
@Bill - you can use a little dental proxa brush or a q-tip and coat the insides of the driver mounting holes with yellow glue to avoid any thread stripping. I'm a big fan of tung oil finishes, but I think these would look nice with a clear finish. You could try some wipe-on poly on some scrap. The variation in that pine grain is mind blowing on some pieces.
Good idea. I usually try to pump a mixture of yellow glue and sawdust, using a toothpick, down the hole, but I have only done this AFTER I have stripped out the hole. Would be much better to do this beforehand!
These stair treads really caught my eye as I was walking past the stack at Menards. And they were only $2 per tread more than the particle board stair treads!!
You might be wondering why I didn't just glue the two 1 inch baffle boards together, making a 2 inch thick composite, before gluing it to the main box. Then I could have flipping the composite 2 inch thick baffle board over and over as needed to cut all the holes and recesses that I needed.
The problem is that almost all of the pine that I have is slightly warped, cupped, and twisted. If I had glued the two baffles into a 2 inch thick composite, it would still have been slightly warped and cupped when the glue set. If I had tried to glue this 2 inch thick baffle to the main cabinet, I may not have been able to develop sufficient clamping pressure to force it flat. But by gluing each baffle individually, I was able to develop enough clamping pressure to force the baffle almost perfectly flat.
Using my two stage process, I now have both 2 inch thick baffles glued to the main box. I set my large two foot square across each baffle for inspection. One baffle is perfectly flat in both directions. No cupping, twisting, or warping of any kind. The other baffle, however, has just a slight cupping, maybe 1/32" or so, toward the center in just one small area. But I should be able to block sand this area perfectly flat using a long, flat sanding block. It is important to get the baffle as flat as possible, otherwise I run the risk of bending driver baskets as I torque the mounting screws.
Those have to weigh a ton. I built my wife a bookcase using 2x10s and boy that was really heavy. These have to be more material than that! I wonder if an electric hand held planer would help or not at this stage. Im interested to see if this wood medium has any advantages being as thick as it is.
Those have to weigh a ton. I built my wife a bookcase using 2x10s and boy that was really heavy. These have to be more material than that! I wonder if an electric hand held planer would help or not at this stage. Im interested to see if this wood medium has any advantages being as thick as it is.
Thanks for the suggestion. I have a hand planer that I will be using to bring down one high spot, but most areas seem fairly flat, now that the glue has set.
In terms of weight, they seem surprisingly light. With the double thick baffle, sides, and bottoms thus far glued into position, each cab weights 27 lbs on my un-calibrated bathroom scales. I have yet to glue the backs on or mount drivers/xover, but I am projecting a total of 40 pounds for each speaker fully assembled. That is not too bad. I can easily carry them up and down from the basement between gluing & cutting operations. (I like to bring the speakers upstairs as this helps the glue dry faster (59F in basement verses 70F upstairs).
Normally, stair treads are 1-1/8 inch thick, but the pine treads at Menards are only 61/64 thick, just a tad less than 1 inch. I have noticed that sometimes the pine used for construction lumber can feel very heavy. And sometimes it can feel very light and wimpy. The density seems to vary quite a bit from lot to lot. All of this wood in kiln dried in some manner, which could also account for the differences.
This is my first project using solid pine to do an entire enclosure. It will also be my last. When thumped, the wood rings pretty much the same as 3/4 MDF or particle board. It will need to be braced heavily. But this is not the main problem. The big problem is the constant warping, twisting, and bending. After working on this enclosure for several weeks, I am beginning to appreciate just how smooth and flat 3/4" MDF, plywood, and particle board are by comparison.
if you are trying stuff, try the danish oil, rub on, three coats should be real nice, not much cheen or shine, and looks very natural, might darken a bit.
BTW my pine had shellac and wax. Will get a pic tonight....
Forgot to mention, it does darken quite a bit, especially if I use the Danish oil with stain mixed in. I tested dark walnut Danish oil and light walnut Danish oil. Both looked very blotchy. Only the natural Danish oil looked good because it darkened more evenly. Bill
if you are trying stuff, try the danish oil, rub on, three coats should be real nice, not much cheen or shine, and looks very natural, might darken a bit.
BTW my pine had shellac and wax. Will get a pic tonight....
Forgot to mention, it does darken quite a bit, especially if I use the Danish oil with stain mixed in. I tested dark walnut Danish oil and light walnut Danish oil. Both looked very blotchy. Only the natural Danish oil looked good because it darkened more evenly. Bill
I've seen line used to demonstrate blotchy wood. Reportedly the best pre-stain conditioner is Charles Neal's product
But Chahly - Stahkist don't want speakers that look good, Stahkist wants speakers that sound good!
Prestain conditioner works well on the 2 x lumber. Its far from perfect. But the bottoms of all those shwlfs have no prestain conditioner and the sides and fronts do. I used chestnut stain oil based and general finishes satin armrseal 3-4 coats.
Thanks for the pics & tips on pre-stain conditioning and gel stains. That really makes a difference! I will add pre-stain conditioning and gel stains to my list of stuff to try out. I have a big pile of knotty pine remnants to work with, but am still waiting for it to warm up a little bit more (Wisconsin weather!). Still too cold for finishing work. When is it going to start hitting 50 degrees???
I just watched a Charles Neal video on blotchy wood staining. So, if I understand what John is suggesting, a gel type stain will produce less blotching because it is thicker and therefore will soak into the wood more evenly . A thinner type of stain will be more blotchy because it soaks into the softer wood pores at a faster rate. A pre-stain conditioner is essentially a sealer that slows down the rate at which any stain soaks in. Would this be correct? Or do I have it backwards?
I made a template for the Neo3W's to allow surface mounting without faceplates. I recessed the raw driver 1/4" and drilled 4 clearance holes for the driver pop rivets (see pics). At a mounting depth of 1/4", the driver surface plane remains flush with the baffle plane. The remaining recessed area around the driver's perimeter is then filled in with the 1/16" thick foam gasket that came with the driver. I will be mounting the drivers with small 4/40 or 6/32 wood screws using the slots that were originally designed to mount the faceplates.
My experience has been that flush mounting is not as important as a smooth transition to the baffle. What you have looks pretty good, the ripples will be small. You can measure the difference by applying tape from the tweeter face to the baffle on your cut out.
The gel stains are also slow to adsorb and because of the high pigment content can act like a paint and help to hide any grain flop.
I built a custom faceting fixture consisting of 3 sections:
1) A large, heavy loudspeaker cradle to hold the speaker at a 45 degree angle. I made this out of 12x48" shelving (see pics).
2) Four intermediate 45 degree angle MDF supporting struts, firmly clamped to the base and top platform.
3) A long, dual MDF top platform with open center slot to support and guide the router. This elongated platform is firmly clamped into a level position from side to side, but is inclined by 4 degrees from back to front to create the facet.
I faceted the baffle in multiple passes, lowing the bit slightly with each pass. It took me several days to build the fixture, but I should be able to use it again on future tower type floor stander projects.
Still have to chip some of those yellow glue drips off the cement floor with a putty knife. I put down paper to keep the glue off the floor, but sometimes the drips miss and hit the floor anyhow!
Still have to chip some of those yellow glue drips off the cement floor with a putty knife. I put down paper to keep the glue off the floor, but sometimes the drips miss and hit the floor anyhow!
Badges of Honor! Paint, stain, glue...That's what a shop is all about! Well done.
You guys that know your way around a wood shop are a constant inspiration to me. Wonderful fixture for tapering
Thanks. I've picked up quite a few woodworking tips from fellow builders in the past few years, attending shows and listening. Credit to the community of fellow builders!!!
Still have to chip some of those yellow glue drips off the cement floor with a putty knife. I put down paper to keep the glue off the floor, but sometimes the drips miss and hit the floor anyhow!
Badges of Honor! Paint, stain, glue...That's what a shop is all about! Well done.
Thanks, Marty. Of course, you should see the huge pile of sawdust underneath my table saw, which is off-camera on the other side of the basement!!!
That's a way I've not seen before, but very well implemented. Very cool, Bill!
Thanks, Ben. I came up with this idea after listening to Keith describe how he made the curved top on his Jedi Mind Tricks subwoofer. His router sled and rail system got me thinking that a modified version of this could be used to make simple, inclined baffle facets. I think he made a "youtube" video describing how he made his system.
Comments
you can use a little dental proxa brush or a q-tip and coat the insides of the driver mounting holes with yellow glue to avoid any thread stripping.
I'm a big fan of tung oil finishes, but I think these would look nice with a clear finish. You could try some wipe-on poly on some scrap.
The variation in that pine grain is mind blowing on some pieces.
Good idea. Not sure if I am going to stain or oil the wood, but if I do, I will give that a try. Even if I leave the wood natural without sealer, oil or anything else, hitting it with lacquer will cause roughness on the first few coats, due to a chemical reaction with the wood itself. I like to sand down the first few coats with 220 until the lacquer starts to build into a very smooth finish.
Good idea. I usually try to pump a mixture of yellow glue and sawdust, using a toothpick, down the hole, but I have only done this AFTER I have stripped out the hole. Would be much better to do this beforehand!
These stair treads really caught my eye as I was walking past the stack at Menards. And they were only $2 per tread more than the particle board stair treads!!
You might be
wondering why I didn't just glue the two 1 inch baffle boards together, making a 2 inch thick composite, before gluing it to the main box. Then I could have flipping the composite 2 inch thick baffle board over and over as needed to cut all the holes and recesses that I needed.
The problem is that almost all of the pine that I have is slightly warped, cupped, and twisted. If I had glued the two baffles into a 2 inch thick composite, it would still have been slightly warped and cupped when the glue set. If I had tried to glue this 2 inch thick baffle to the main cabinet, I may not have been able to develop sufficient clamping pressure to force it flat. But by gluing each baffle individually, I was able to develop enough clamping pressure to force the baffle almost perfectly flat.
Using my two stage process, I now have both 2 inch thick baffles glued to the main box. I set my large two foot square across each baffle for inspection. One baffle is perfectly flat in both directions. No cupping, twisting, or warping of any kind. The other baffle, however, has just a slight cupping, maybe 1/32" or so, toward the center in just one small area. But I should be able to block sand this area perfectly flat using a long, flat sanding block. It is important to get the baffle as flat as possible, otherwise I run the risk of bending driver baskets as I torque the mounting screws.
Sehlin Sound Solutions
Thanks for the suggestion. I have a hand planer that I will be using to bring down one high spot, but most areas seem fairly flat, now that the glue has set.
In terms of weight, they seem surprisingly light. With the double thick baffle, sides, and bottoms thus far glued into position, each cab weights 27 lbs on my un-calibrated bathroom scales. I have yet to glue the backs on or mount drivers/xover, but I am projecting a total of 40 pounds for each speaker fully assembled. That is not too bad. I can easily carry them up and down from the basement between gluing & cutting operations. (I like to bring the speakers upstairs as this helps the glue dry faster (59F in basement verses 70F upstairs).
Normally, stair treads are 1-1/8 inch thick, but the pine treads at Menards are only 61/64 thick, just a tad less than 1 inch. I have noticed that sometimes the pine used for construction lumber can feel very heavy. And sometimes it can feel very light and wimpy. The density seems to vary quite a bit from lot to lot. All of this wood in kiln dried in some manner, which could also account for the differences.
This is my first project using solid pine to do an entire enclosure. It will also be my last. When thumped, the wood rings pretty much the same as 3/4 MDF or particle board. It will need to be braced heavily. But this is not the main problem. The big problem is the constant warping, twisting, and bending. After working on this enclosure for several weeks, I am beginning to appreciate just how smooth and flat 3/4" MDF, plywood, and particle board are by comparison.
Bill
Thanks Scott. And thanks again for posting the detailed info, making a project like this possible!!
Does the pine have any saving graces? Does it smell a whole lot better that MDF? That's one thing I enjoy about hardwoods.
Yea, time to get out the broom and clean up a little!!
It does smell much better than MDF. And much, much less dust!! But I liked the smell of the walnut even better.
Reportedly the best pre-stain conditioner is Charles Neal's product
before and after
I made a template for the Neo3W's to allow surface mounting without faceplates. I recessed the raw driver 1/4" and drilled 4 clearance holes for the driver pop rivets (see pics). At a mounting depth of 1/4", the driver surface plane remains flush with the baffle plane. The remaining recessed area around the driver's perimeter is then filled in with the 1/16" thick foam gasket that came with the driver. I will be mounting the drivers with small 4/40 or 6/32 wood screws using the slots that were originally designed to mount the faceplates.
The gel stains are also slow to adsorb and because of the high pigment content can act like a paint and help to hide any grain flop.
A little progress:
I built a custom faceting fixture consisting of 3 sections:
1) A large, heavy loudspeaker cradle to hold the speaker at a 45 degree angle. I made this out of 12x48" shelving (see pics).
2) Four intermediate 45 degree angle MDF supporting struts, firmly clamped to the base and top platform.
3) A long, dual MDF top platform with open center slot to support and guide the router. This elongated platform is firmly clamped into a level position from side to side, but is inclined by 4 degrees from back to front to create the facet.
I faceted the baffle in multiple passes, lowing the bit slightly with each pass. It took me several days to build the fixture, but I should be able to use it again on future tower type floor stander projects.
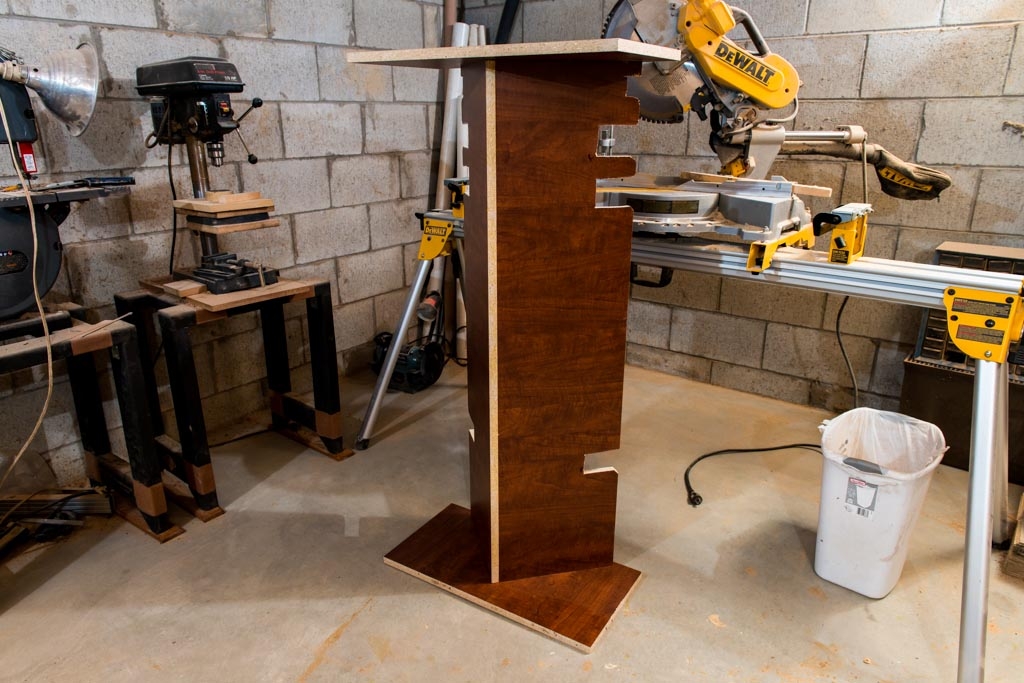
Still have to chip some of those yellow glue drips off the cement floor with a putty knife. I put down paper to keep the glue off the floor, but sometimes the drips miss and hit the floor anyhow!
Wonderful fixture for tapering
Badges of Honor! Paint, stain, glue...That's what a shop is all about! Well done.
InDIYana Event Website
Thanks. I've picked up quite a few woodworking tips from fellow builders in the past few years, attending shows and listening. Credit to the community of fellow builders!!!
Thanks, Marty. Of course, you should see the huge pile of sawdust underneath my table saw, which is off-camera on the other side of the basement!!!
Thanks, Ben. I came up with this idea after listening to Keith describe how he made the curved top on his Jedi Mind Tricks subwoofer. His router sled and rail system got me thinking that a modified version of this could be used to make simple, inclined baffle facets. I think he made a "youtube" video describing how he made his system.
A little progress:
I flush mounted the ND140's, Neo8's, and Neo3's.