The NLA7 project is one of a number of speakers built around a NLA Peerless 830862 5 1/4" Nomex woofer and various tweeters. This pair used the CSS LD22C tweeters I picked up used at DIY Iowa 2018. The .5 cu. ft. cabinets were built using Baltic birch plywood veneered with quarter sawn cherry and the tops and bottoms were trimmed with cherry hardwood. I didn't do a great job documenting the build but the previous NLA build in walnut used the same techniques so I'll use some of those pictures here.
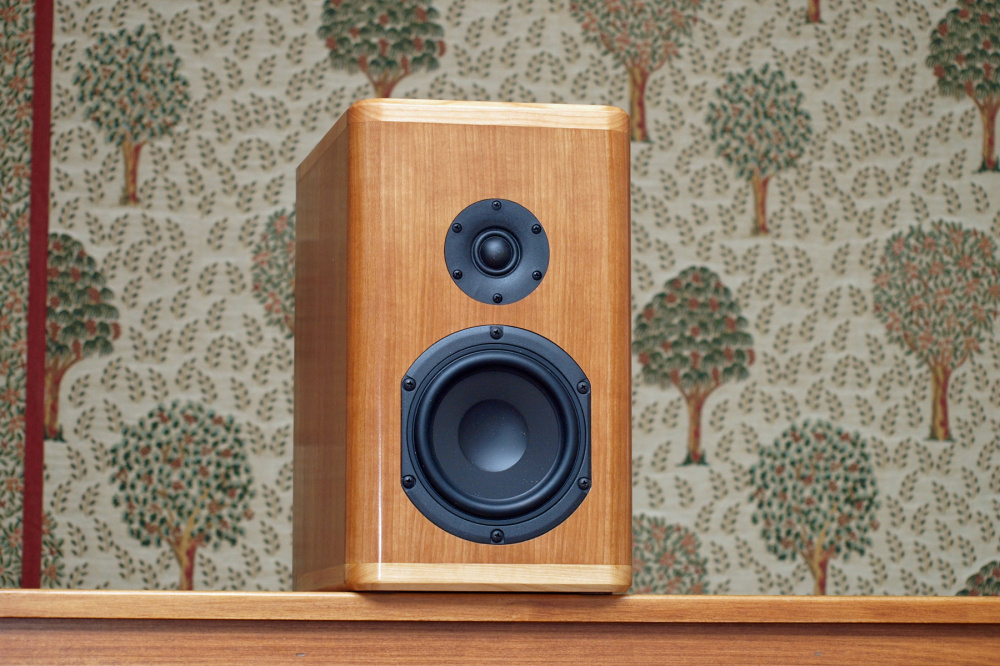
Box sim.
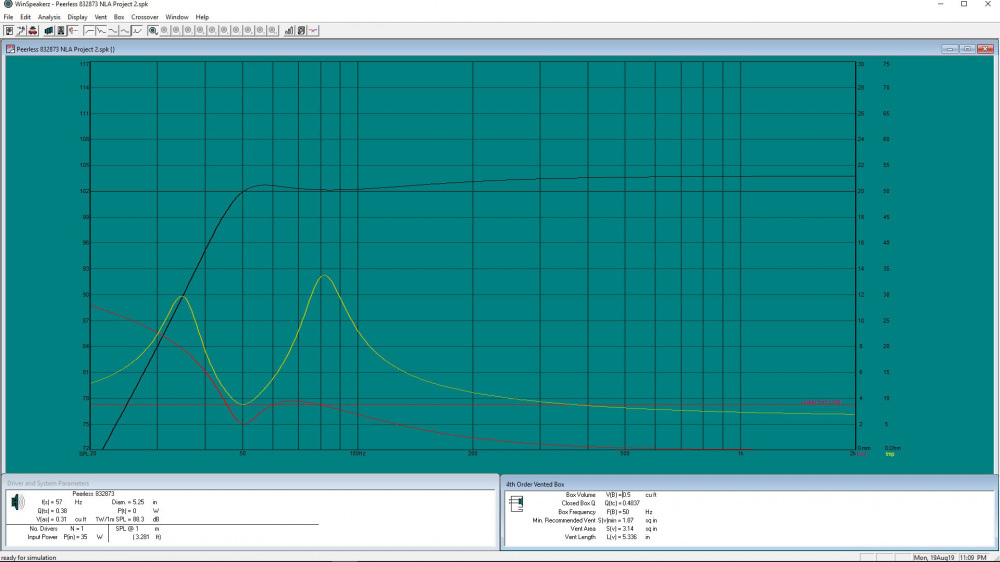
Since I had enough woofers to build 5 pairs I cut enough parts for all of them.
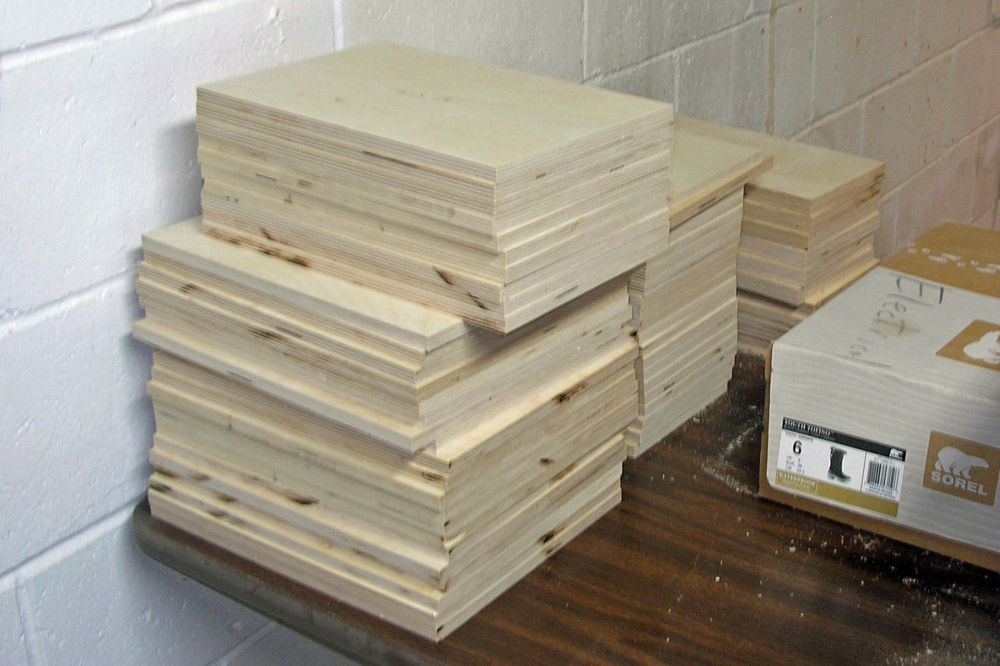
I glued up all the boxes except the tops and bottoms at once.
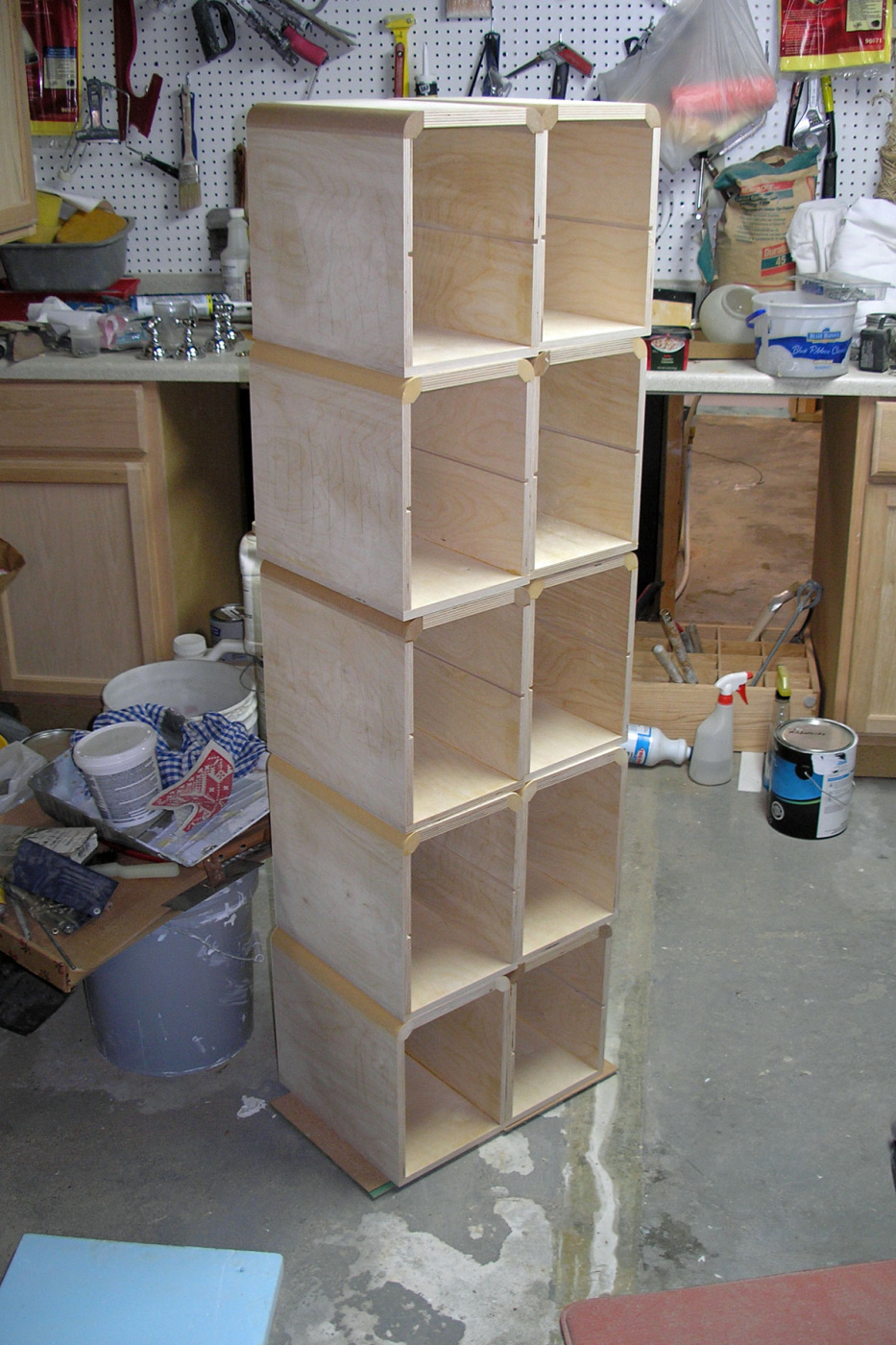
The boxes have 1/2 inch sides and backs with 3/4 baffles. I used 1 1/8" MDF stair treads to make the corners which I find machines the round overs without the tear out problems I've had with plywood. The 1/4" dado in the side is for a piece of plywood that gets tied to the other side as a brace.
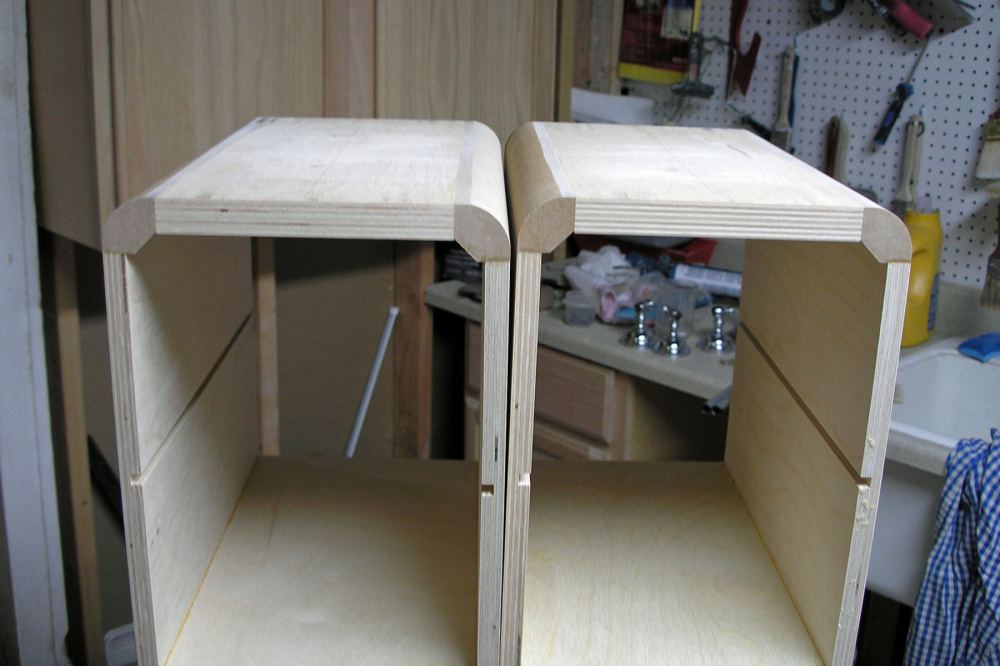
The hardwood trim for the tops and bottoms were glued to the plywood sides first and were sized to be just slightly larger than the boxes. These pieces of trim were left long at glue up and then the panels were cut to length. The trim was also left slightly proud of the plywood and flush trimmed on a router table.
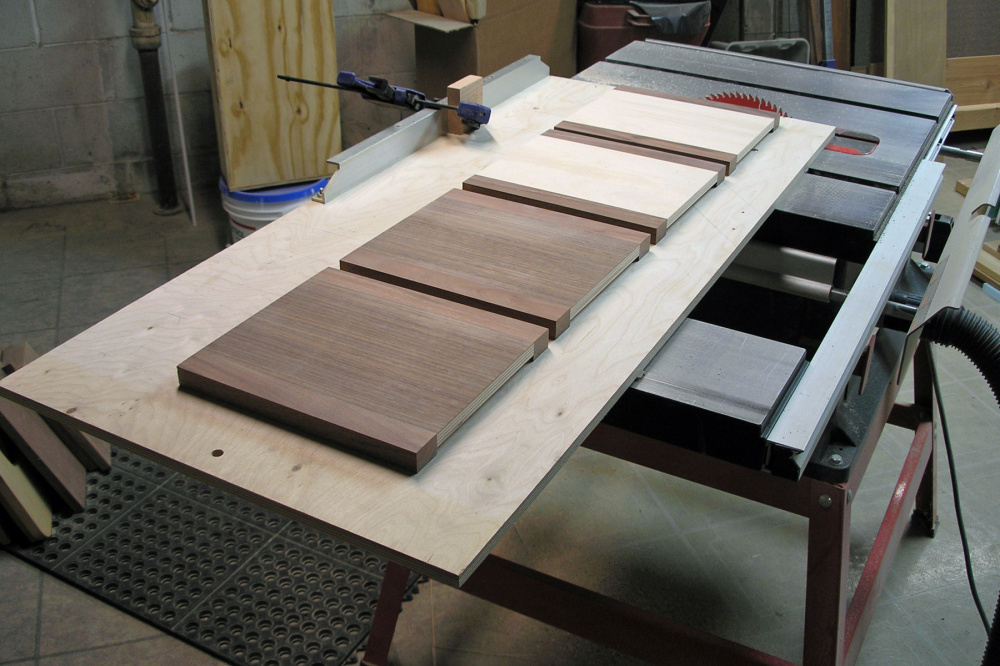
The rest of the trim was glued using the same technique. The cross grain trim pieces are left slightly long and get trimmed to size after they are glued to the boxes.
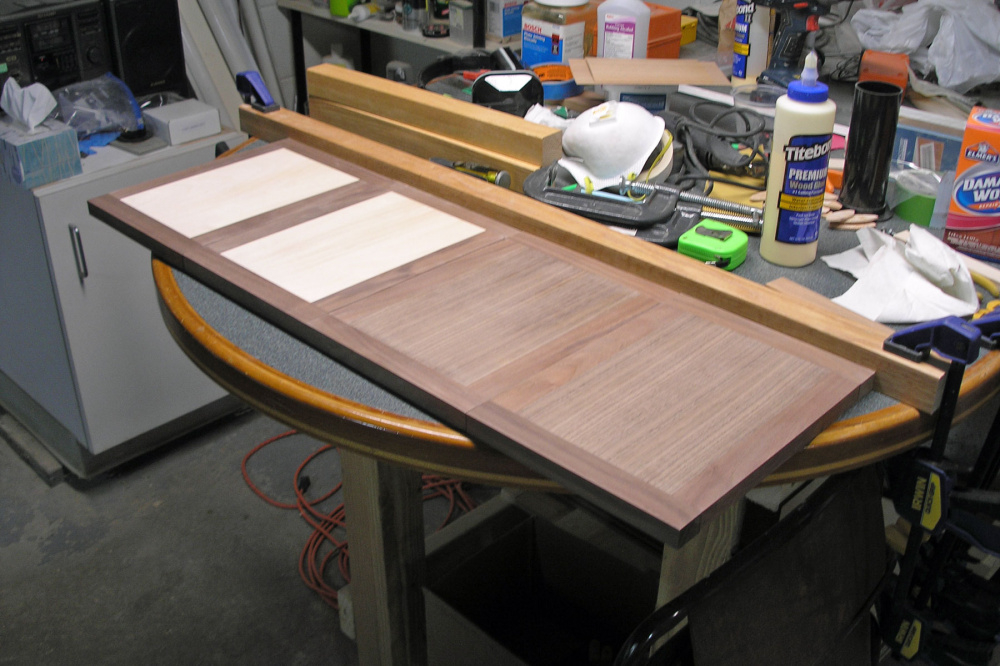
The tops and bottoms are positioned in place and some small scraps of wood are placed inside the boxes in the corners with double stick tape. This keeps the tops and bottoms from floating out of place when gluing. I do this with both tops and bottoms before starting glue up.
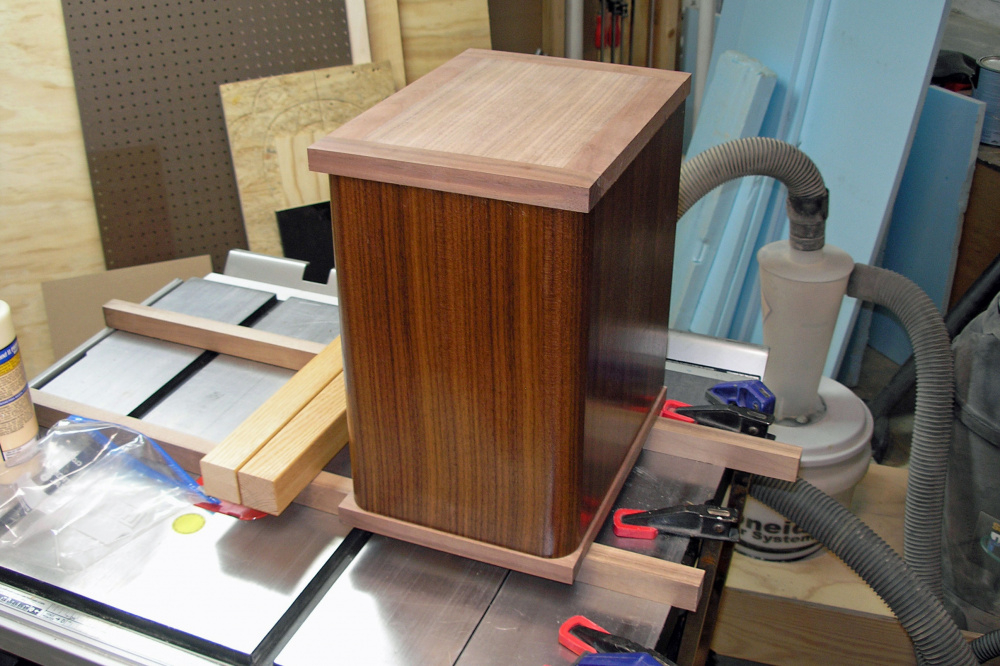
Gluing the tops and bottoms on.
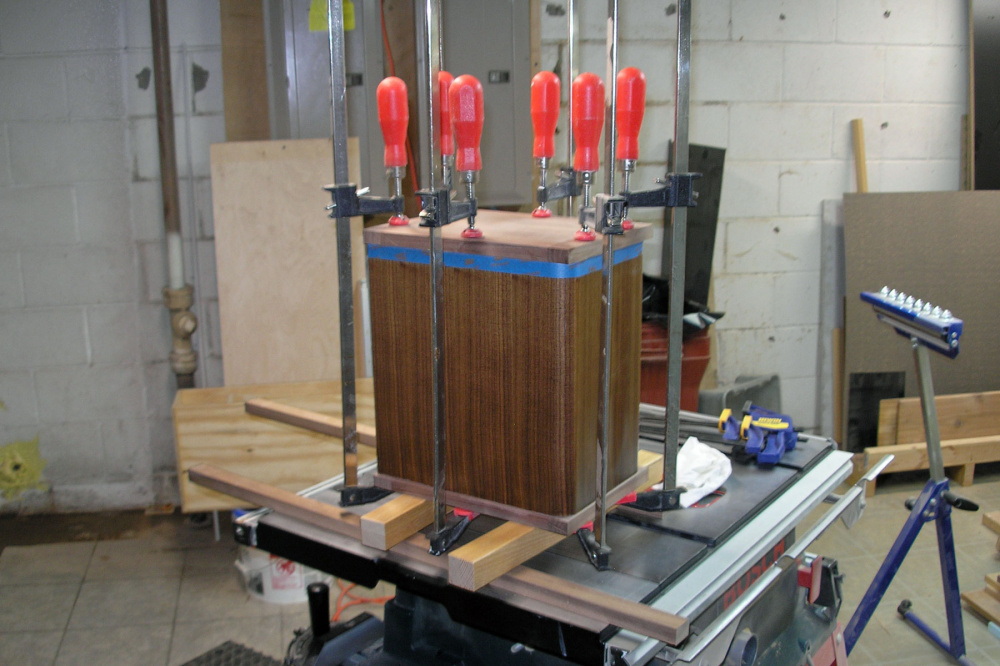
The tops and bottoms were trimmed to match the boxes on a router table with a flush trim bearing bit and then a chamfer was applied with a 45 degree bearing bit.
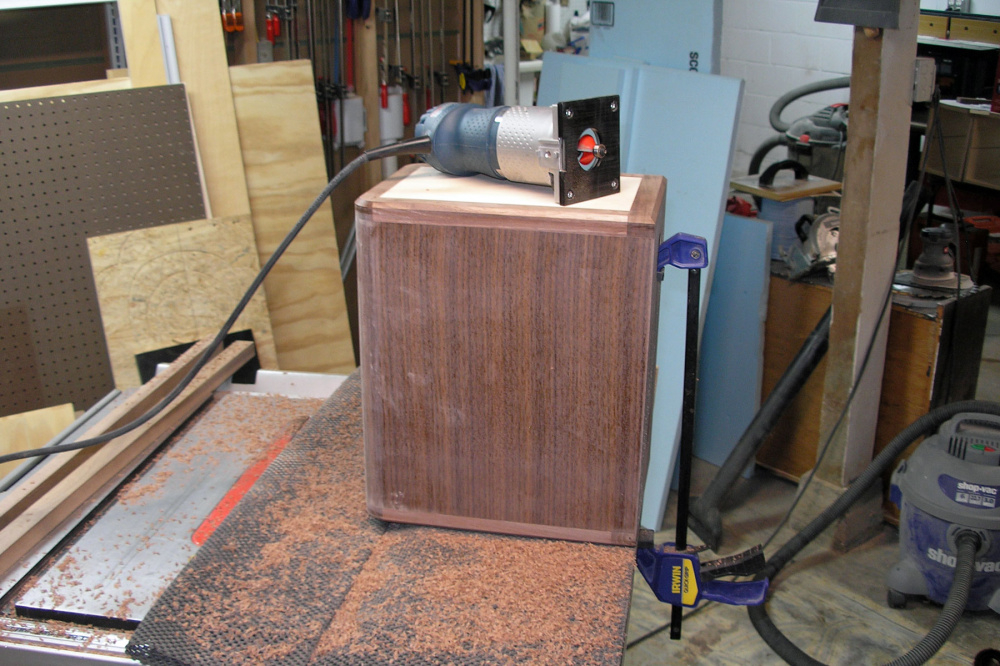
Rebate were cut using templates attached with double sided tape.
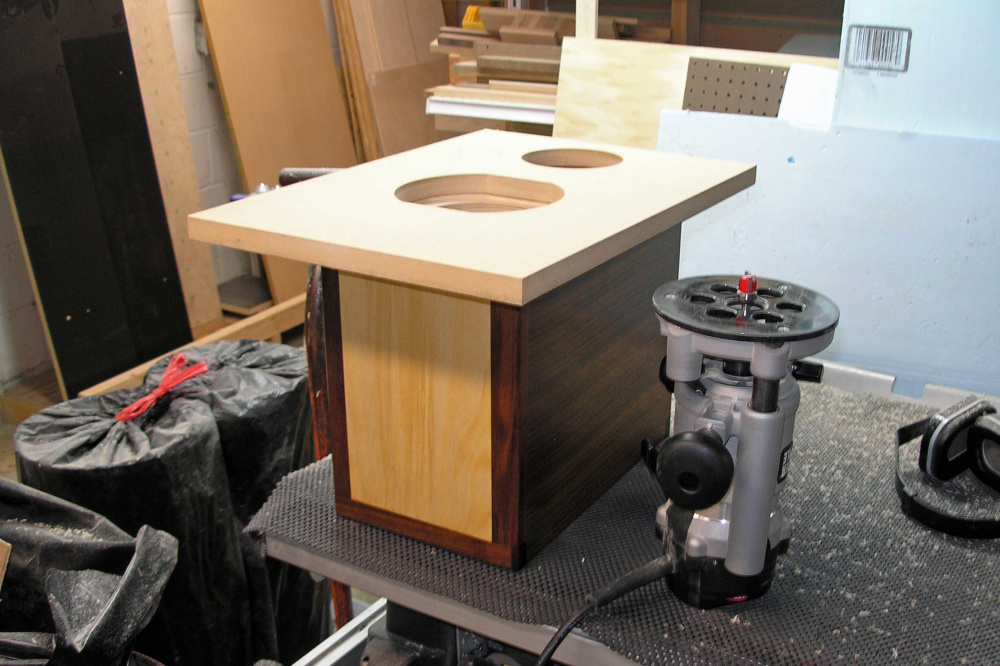
You can see the bracing detail in this picture of the finished rebates.
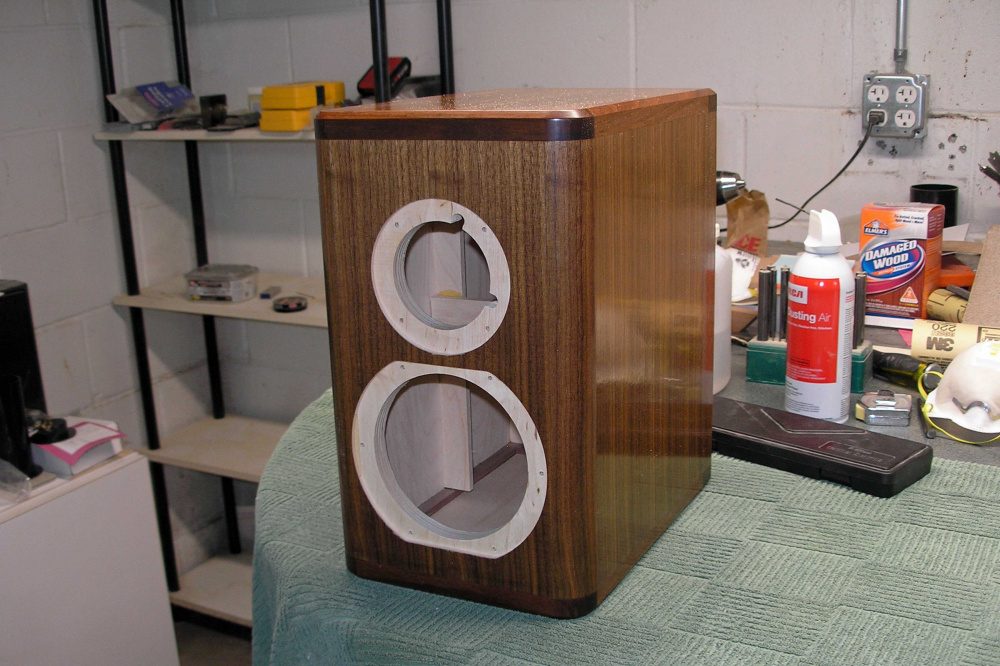
The boxes were finished with a coat of Watco natural Danish oil finish and after waiting the required 72 hours many coats of wipe on poly were applied.
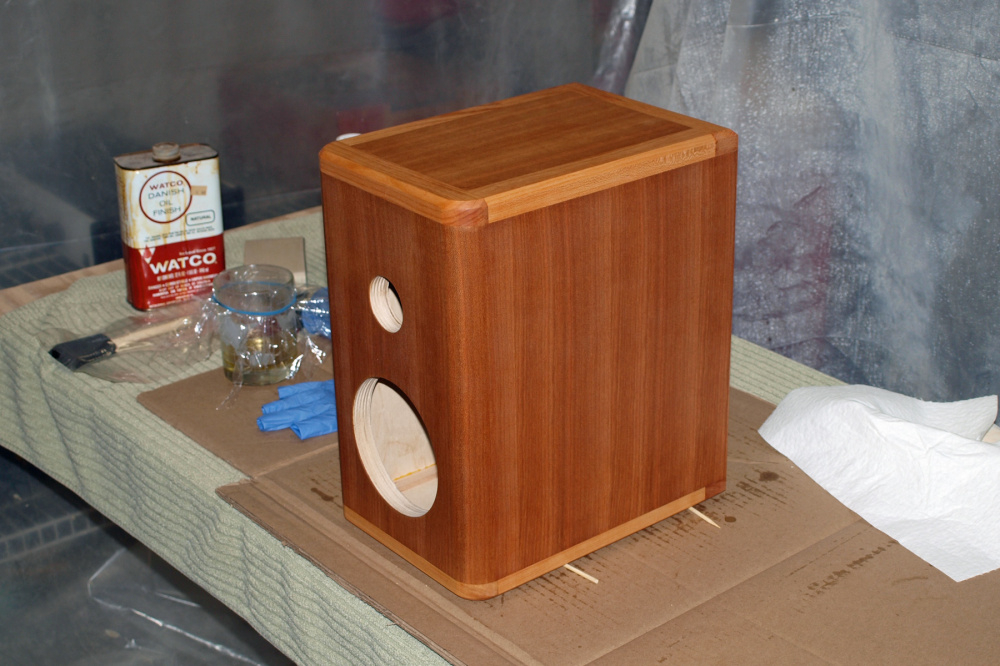
The inside of the front and backs of the cabinets were lined with 1" foam and all other sides were lined with 1" thick UltraSonic Acoustic Panels. Drivers were measured in box and the crossover was designed with the drivers installed in the finished boxes.
FR sim.
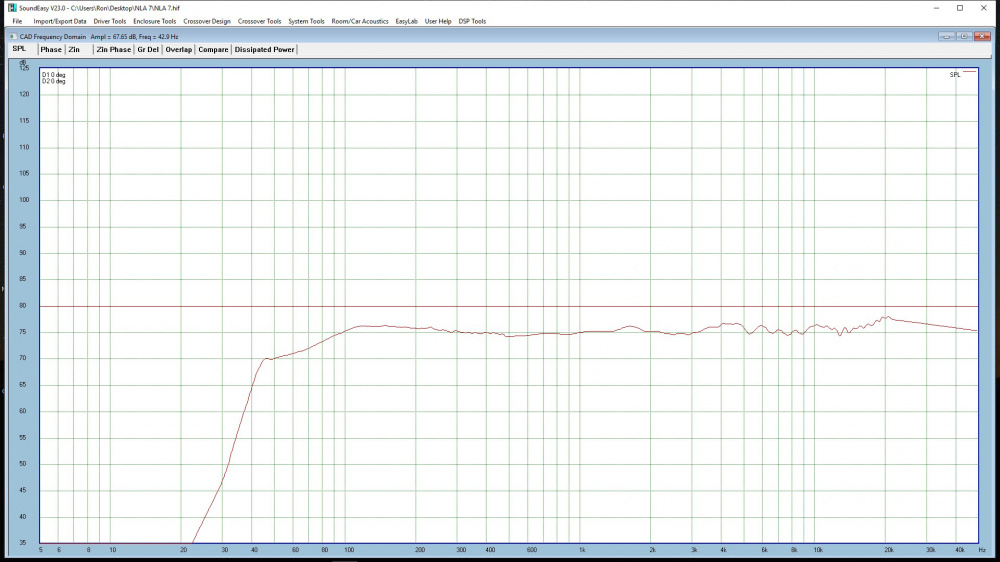
Impedance sim.
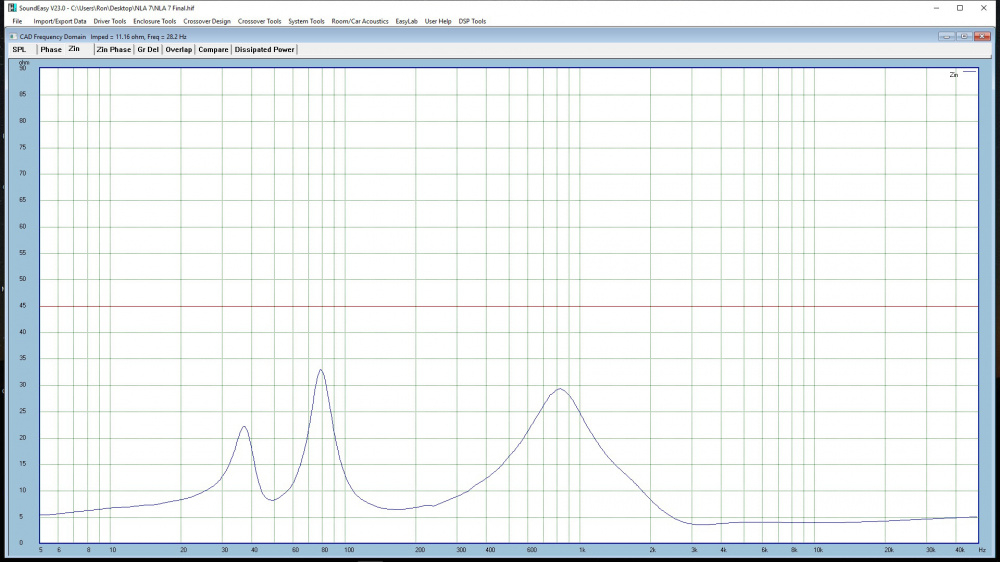
The 24db/oct LR crossover at 2500Hz.
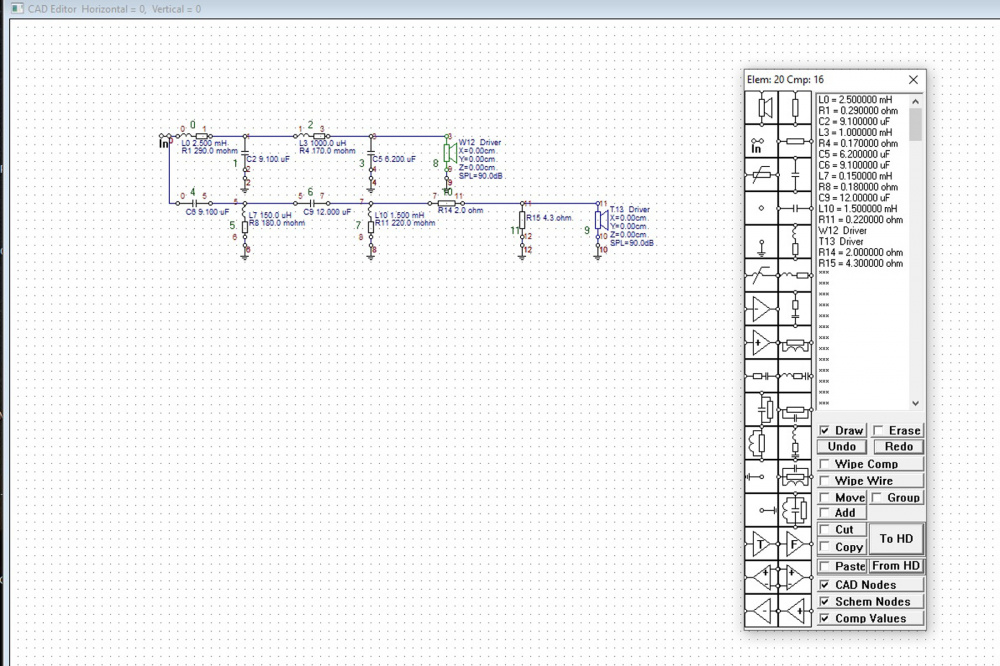
Crossovers.
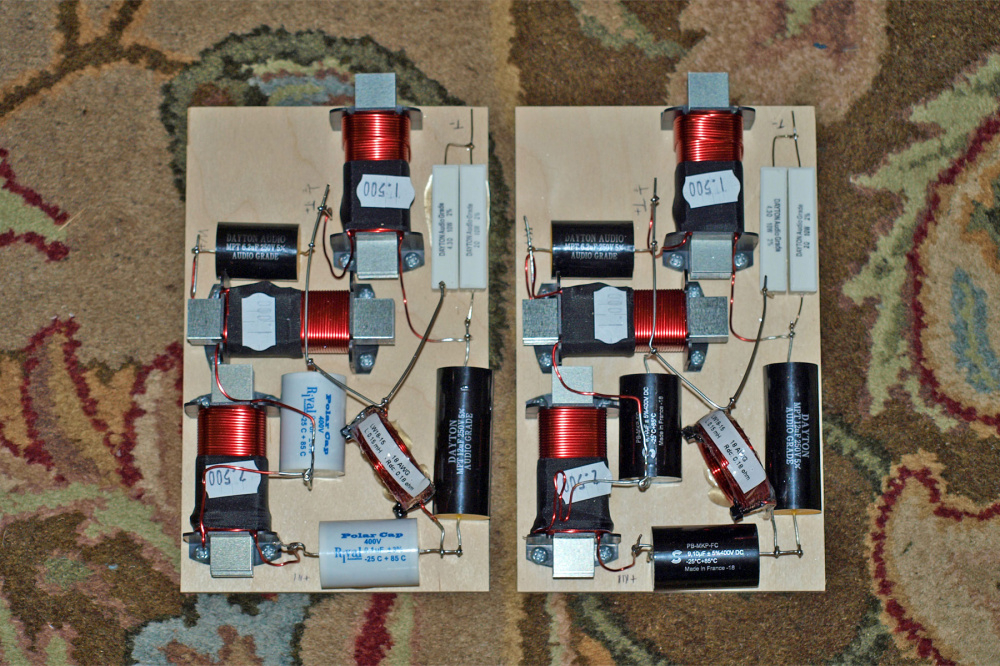
Woofer NF, FF and port measurement.
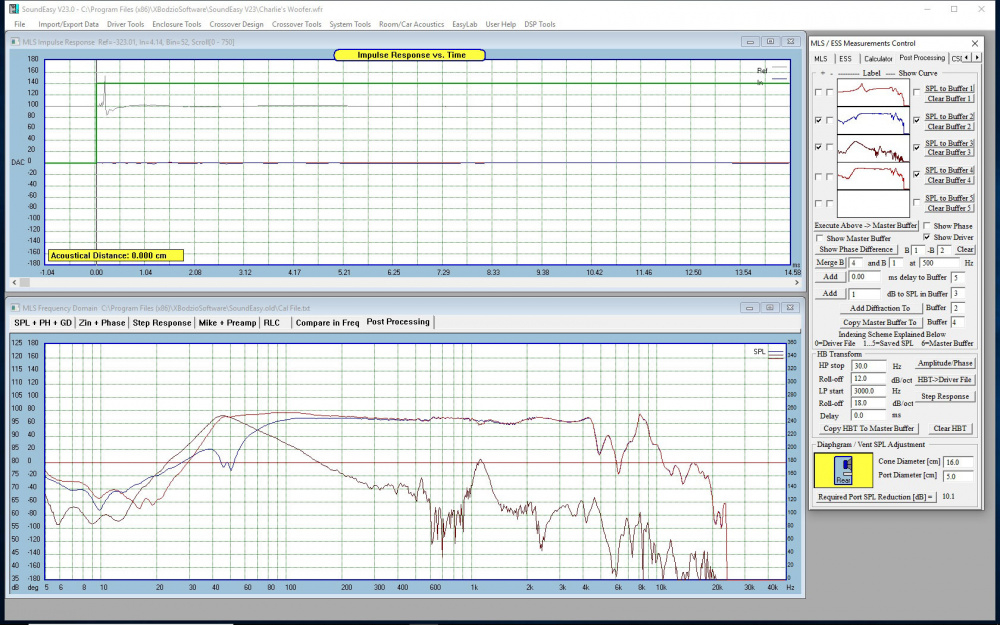
System IM FF good down to 200Hz.
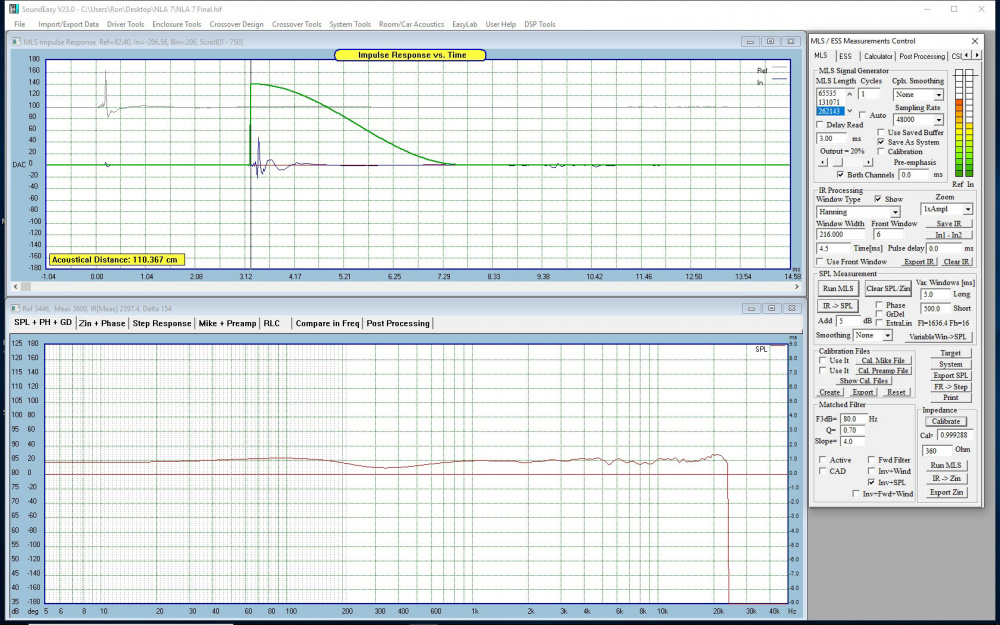
System FF 1M response with reverse null.
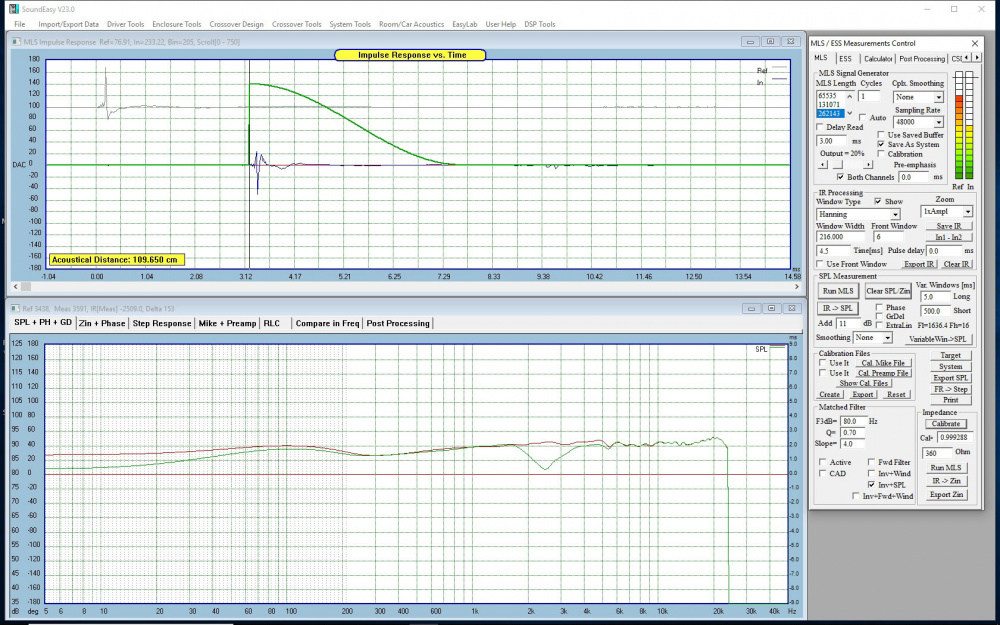
You can find a PDF of the technique I use to veneer around corners here.
https://drive.google.com/open?id=19d0A4yy2WD4yE2v91RbkQ8-UaSdeuve2 Ron
Comments
Now that's a little trick worth copying. As usual, these sure sounded and looked great Ron!
Ron
Peerless still makes the 6 1/2" Nomex and I like it too. They seem to have a more modest breakup than the aluminum drivers and are easy to work with. I'm just about out of the 5 1/4's and will probably be building something with Fountek aluminum cones.
Can you remind me which speakers were yours?
Ron
Ron