Hey guys,
We wanted to share some early pictures of our cabinets we are having made for the Model P215. We are looking at making some nice, reasonably priced production cabs for these kits and offering in two standard finishes. I'm not sure yet on final price, but they should look awesome once complete. These will be finished in satin white automotive and natural satin walnut. Probably not something that many people here will be interested in buying but figured you'd appreciate the construction

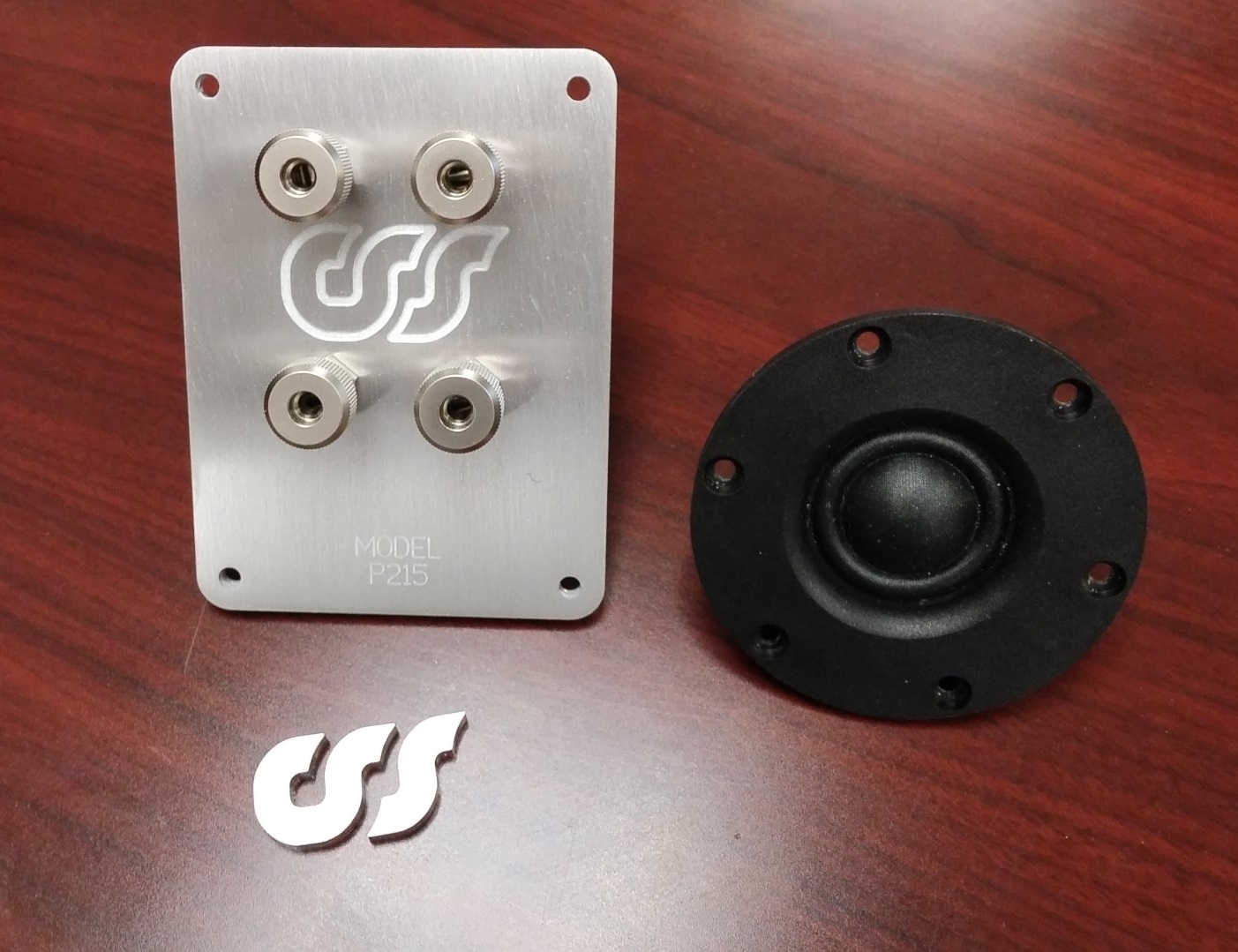
Comments
InDIYana Event Website
- Kerry
Dan
I've done complete 45 degree, tape, and fold up boxes for the smaller speakers. My preference is to keep the front baffle separate. That allows the use of some fancy hardwood or rear mounted drivers.
Tape has been very easy. I only got into trouble trying to add clamps plus tape. Once I pushed one panel out of place everything went to hell. Now it's just tape and checking square
I'll keep looking for the video
The bad thing about PVC is it seems gets statically charged when cut so the particles stick to everything.