I started these a few months back, because I wanted to take a break from my more complex builds, and build a simple 2 way with drivers that I had on hand. I'm still plugging away on my minions build, but these are much simpler, just a rectangle crafted from left over wood scraps, and utilizing a Hivi d6.8b and a Dayton RST28f in the visaton wg that has been used a bunch of times-nothing ground breaking here. One thing that I did notice is that in using a combination of plywood and mdf in the cabinet, it seems to be less resonant, or maybe it's just my imagination. I don't have any proof.
These were designed to be used with the grill on, and maybe it will provide some ideas for those who would like to use a grill, as these were constructed with just a table saw and router with a circle jig. I should also state that these were a quick and dirty build... 50/50's. Look great from 50 feet or 50 mph.
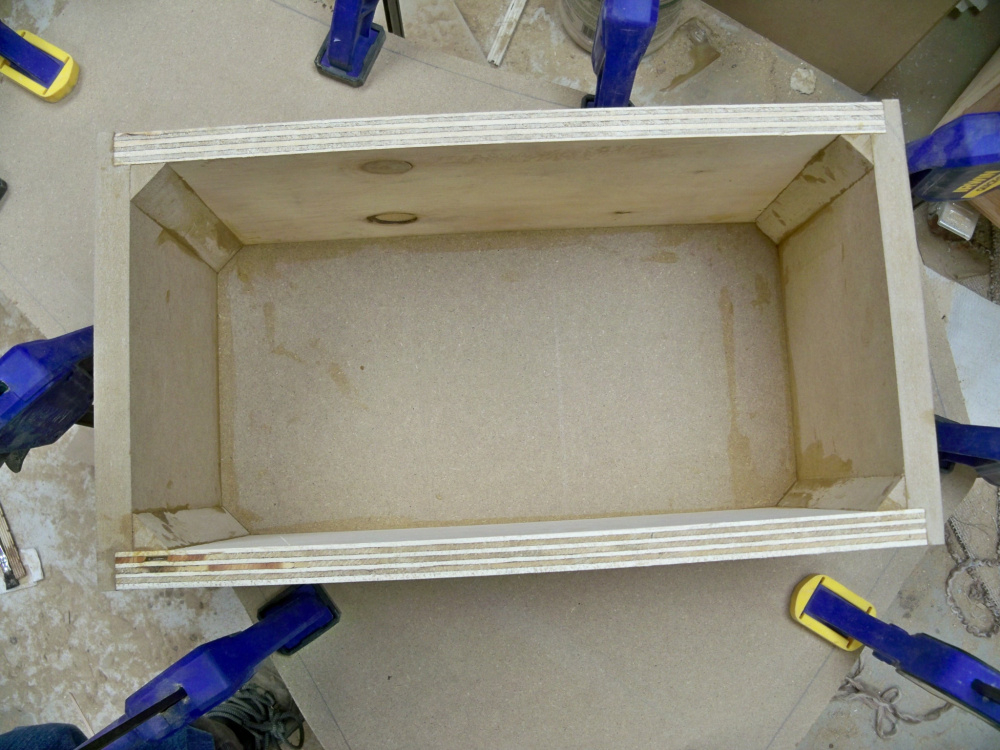
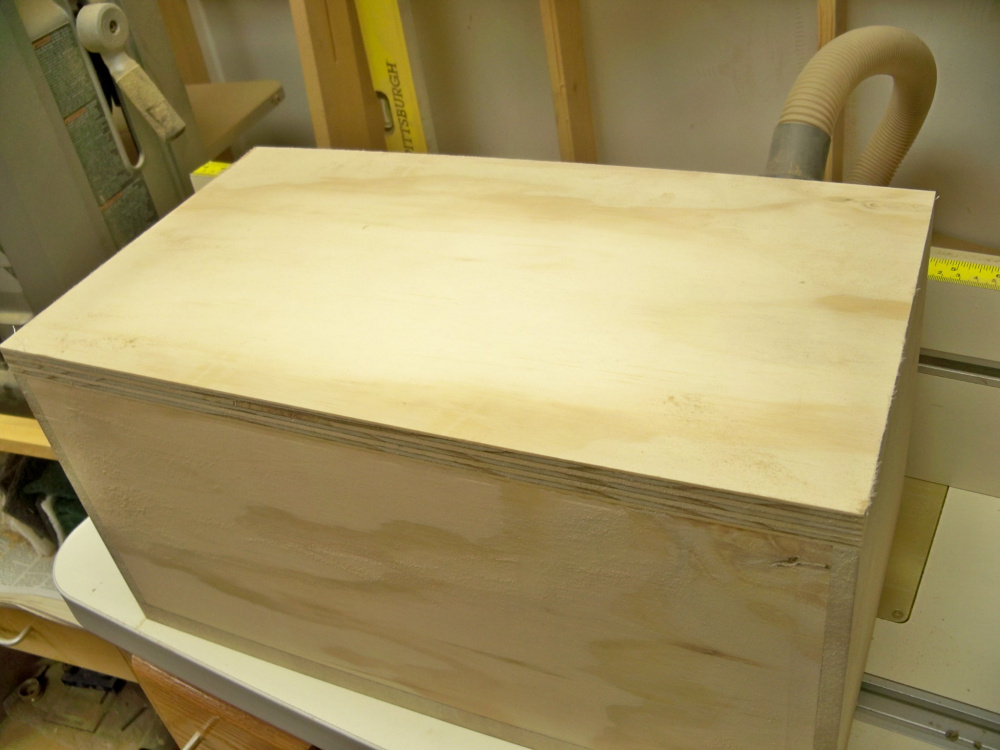
Comments
I agree, and to an extent, reserve the right to disagree. They are materials other than wood with vastly varying properties, and combinations of these materials could result in smaller contributing resonances regardless of bracing ... in certain situations. Stressing a panel also changes its resonance. Ceteris paribus of course.
BTW,how DID you cut the roundovers? 1 1/2 inch router bit? Use a router table?
The roundovers were cut on a router table with 1-1/2 bit.
The glossy finish is automotive urethane clear. Lots of sanding and buffing.
The satin black front is also urethane.
They are far from perfect, but look good from a distance.
No naked drivers for you! I find that I get tired of exposed drivers after the newness wears off, and generally prefer the look of grills in the long run, but that being said I also have several builds that are naked.